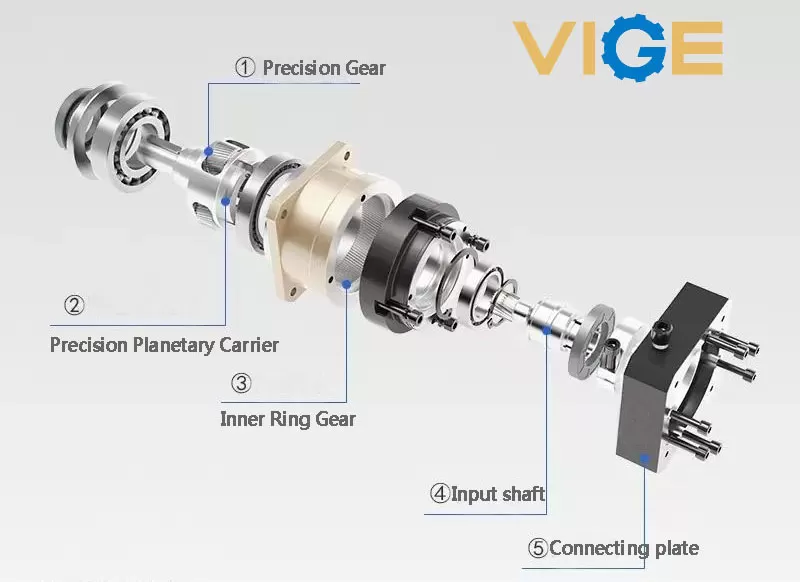
Regularly change the lubricating oil
Change the oil regularly according to the operating instructions and working conditions, to ensure the internal cleanliness and reduce wear. Generally, the first change is required after 220 hours of operation, and then it is changed regularly according to the actual situation. The lubricating oil replaced each time should be better than the previous one. The residual dirty oil needs to be removed before replacement.
Pay attention to the selection of lubricating oil. Different models and specifications of planetary redycer, may require different lubricating oil. Use grease or lubricating oil of recommended models and values.
For vertically installed reducers, if the lubricating oil cannot ensure reliable lubrication of the upper bearing, additional lubrication measures need to be taken.
Regularly check the parts
Check whether the gears are worn. If worn or damaged, they should be replaced or repaired as soon as possible to avoid the expansion of the fault. It can be judged by observing the surface condition of the gears and listening to the running sound.
Check the sealing performance and the integrity of the protective cover to ensure that the internal parts of the reducer are not invaded by sewage to avoid mechanical failures or safety accidents. If the protective cover is damaged, it should be replaced in time, and leakage at the seal should be repaired in time.
Check whether the fasteners are loose. Loose fasteners will cause increased vibration and noise, affecting the normal operation of the reducer. If they are found to be loose, they should be tightened in time.
Pay attention to the operating conditions
Pay attention to the working load of the planetary reducer. The working load during the running-in period generally does not exceed 85% of the rated working load to prevent the reducer from overheating due to long-term continuous operation.
Choose lubricating oil reasonably, especially for reducers with large input power, suitable lubricating oil should be injected, and the oil level and quality of lubricating oil, hydraulic oil, coolant, and the sealing performance of the whole machine should be checked frequently.
Daily cleaning and protection
Keep the reducer clean, clean dust and oil stains on the surface and additional components in time to prevent impurities from entering the reducer and affecting performance.
When the storage period of the reducer exceeds one year, it needs to be treated with anti-rust treatment. Anti-rust oil and other measures can be applied to prevent rust.
Operation and use specifications
Operators should receive professional training and guidance, fully understand the structure and performance of the planetary reducer, and obtain certain operation and maintenance experience before operation.
It is forbidden to use unqualified or deteriorated lubricants to avoid damage to the reducer due to lubricant problems.
Strictly implement the safety operating procedures. During the operation of the equipment, the rotating parts shall not be cleaned or repaired. Materials unrelated to the operation of the equipment shall not be stored on site, and the site shall be kept unobstructed.
Regularly check the operating conditions
During the patrol inspection, pay attention to whether the planetary reducer has abnormal vibration under normal load, whether the temperature instrument indication of each bearing is normal, whether the oil supply pressure and flow of the lubrication system meet the requirements, whether the equipment has abnormal noise, and whether there is any odor in the mechanical and electrical parts.
When the machine is shut down for a long time, pay attention to dust infiltration and rust generation. Start the planetary reducer at least once a month, run it for a period of time each time, and observe the rust of the gears and bearing brackets.